Extruded & Spliced Rubber Gaskets & O-rings
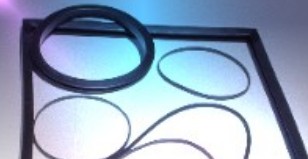
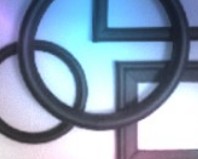
Our fabrication department produces custom Extruded and Spliced Gaskets with Cold and Hot Vulcanized seams to meet your specific sealing requirements. We can vulcanize one of our Standard Profile Rubber Extrusions or a custom custom profile rubber extrusion for your specific application. We manufacture Extruded and Spliced rubber gaskets and seals from both solid and sponge materials and a variety of compounds including Neoprene, EPDM, Nitrile, Viton and Silicone. We offer standard commercial grade materials and specification grade materials to meet Military, FDA and ASTM Specifications. From simple rings to complex door gaskets, we have the experience and expertise to provide the ultimate sealing solutions for your application.
-
-
Splicing Methods
-Spliced O-rings
-Small and Large Gaskets
-Large Runs
-Vulcanized Corners
-40 to 90 Durometer
-Small Runs
-Custom Compounding
-ASTM D2000 Materials
-ASTM D1056 Materials.
-ASTM D2000 specs
-Standard Profile Options
-Cut To Length
-Mil-Spec Materials
-Punching
-Notching
-Gasket Kits
-Special Packaging
-Part Marking



Please use the links above to get your project
started or call 770-736-0332 to discuss your project
with a sealing specialist.
Butt Splice-
a common method used for fabricating endless gaskets where there is limited or no strain on the splice.
Bevel-
this splicing method is used as an alternative to the butt splice if the cross sectional area does not allow for a suitable bond using the butt splice.
Step Splice-
used where a maximum bond strength is required, yet permitting nominal deformation under compression or tension when.
Corner Splice-
used to form gaskets of special configurations. They provide a satisfactory static seal where the splice is not under a strain.
Molded Splice-
Many gaskets and seals can be produced economically by splicing extruded shapes to form complete gaskets.
Vulcanizing/ Hot Splicing
A rubber extrusion around a window opening is often the best way to keep the rain and wind out. Regional Rubber uses the hot splicing/vulcanizing process to chemically bond two ends of a rubber extrusion together. By creating an endless seal, the gasket is more impermeable to the elements. This is especially important when a moving vehicle is involved due to flexing of the parts. The bond is longer lasting and maintains its elastic properties.